Regulatory enforcement is ramping back up to pre-pandemic levels and the risk of drug recalls is on the rise with it. There were 94 drug recall events during the second quarter of 2022 — higher than all but one other quarter in the past three years, according to a quarterly report by Sedgwick, a tech-enabled solutions company for employers.
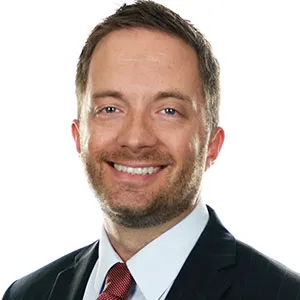
“I don't think there's going to be any massive change in the number of recalls for the year. I think it'll probably continue to be steady. But based on where we're at, we could surpass a five-year record,” Chris Harvey, senior vice president at Sedgwick, says.
One factor driving this uptick is a change in how the FDA conducts inspections. During the pandemic, the FDA switched from relying on in-person inspections to using digital tools, such as remote regulatory assessments.
Initially, there was a considerable learning curve for both inspectors and companies, as the process was clunky and difficult. But today those kinks have largely been ironed out and remote assessments have become more streamlined, Harvey says.
“There's the potential to become more efficient with [remote assessments], less travel, the potential for more inspections, the potential to mine the data faster, [and] to identify things that may have been missed in previous years,” Harvey says.
Electronic data reviews also offer FDA inspectors a better means of identifying anomalies, he says.
“I think the FDA has gotten used to, and are utilizing, different and new tools now for their remote inspections, their remote audits and electronic audits,” Harvey says. “So, I think they're having better visibility into what companies are doing as well. That could be a contributing factor to what we're seeing this year as far as an increase in the number of pharma recalls.”
Identifying problem areas
Companies that manufacture over the counter (OTC) drugs should pay particular attention to recall risk related to these remote reviews.
“A significant percentage of warning letters in the second quarter of 2022 went to OTC drug companies, compounding pharmacies and outsourcing facilities. It is expected that a focus on OTC manufacturers for these types of reviews will continue,” states the Sedgwick report.
Overall, recalls in Q1 were at the same level as Q2. But, the number of units recalled was higher in Q1, solely due to the fact that three were large recalls of OTC drugs.
One acetaminophen recall, for example, included more than 300 million units. Another recall for a cold medicine impacted more than 60 million units, while a third involving another brand of acetaminophen pulled more than 25 million units off shelves.
“So, those three recalls alone were the anomaly that really drove those volumes,” he says.
Most often drug recalls are the result of Current Good Manufacturing Practice (cGMP) deviations. In Q2, cGMP deviations, such as problems with impurities, failed specifications and sterility issues led the pack, according to the report.
“Mislabeling is another big one,” Harvey says.
Many of these problems, such as having the wrong lot number or the wrong expiration number on the packaging, can be avoided with proper diligence.
“And obviously, there's a greater impact when those type of issues happen on the OTCs that have these large batches sizes,” Harvey says.
Reducing recall risk
To steer clear of thorns, Harvey says companies should be diligent about auditing their internal processes and assessing legal risks related to drug recalls. They should also take the time to scan FDA enforcement reports and warning letters to identify where similar companies with similar products ran into trouble, Harvey says.
“The environment that we're in today, there's a high demand for product, there are supply chain issues, and there are labor shortages. So, all of those can be a mixture of disruptions that companies have to navigate and stay diligent for,” Harvey says.
If companies are experiencing supply chain problems, carefully vetting alternatives is crucial. Ensure not only that a product is validated and certified initially, but that monitoring continues over time. As Harvey notes, suppliers sometimes make changes and fail to notify the company.
“Companies really need to look at supplier verification, [and] here they may be vulnerable,” Harvey says.
Organizations should also try to sidestep unforced errors. In the face of labor shortages, there’s a temptation to skimp on training to save time and get employees onboarded quickly. But cutting corners can lead to gaps that cause headaches down the road.
“It's critical for companies to continue to have a strong corporate culture regarding quality and not to take shortcuts based on the high demand, because that's where you could have issues,” Harvey says.
Internal recall plans and procedures should also be reviewed. As Harvey notes, some organizations haven’t updated their recall plans in years.
“Occasionally I’ll run across a recall plan that was written 15 years ago that still references faxing,” he says.
Harvey also recommends that companies focus reviews not only on internal plans, but also those related to the rest of the supply chain. And just as important as updating internal protocols are modifications to protocols and contracts with customer-facing companies.
“How do the pharmacies engage in a recall situation? How do they want to engage in a recall situation?” Harvey says. “All of that can be important based on how the environment has changed the last few years.”
Another area organizations should keep an eye on is cybersecurity, Harvey says. One of the most common strategies a hacker might use is breaching the system and holding it for ransom until they are paid to bring it back online.
“Pharmaceutical companies need to maintain very good security levels to reduce or mitigate an opportunity for any kind of breaches,” he says. “Recalls can cause drug shortages, but you don't want breaches causing those as well.”